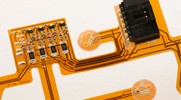
In the realm of modern electronics, wire harness assembly plays a crucial role in ensuring the smooth functioning of various devices and systems. While often overlooked, this intricate process, along with flex circuit manufacturing, forms the backbone of electronic equipment. In this blog, we will delve into the significance of wire harness assembly and shed light on its importance in today's technological landscape.
1.Understanding Wire Harness Assembly: Wire harness assembly refers to the process of organizing and integrating wires, cables, and connectors into a single unit. It involves precise routing, bundling, and securing of electrical components to facilitate efficient transmission of signals and power within electronic systems.
2.Key Components of Wire Harness Assembly:
•Wires and Cables: These are the essential conductive elements that carry electrical signals or power from one point to another.
•Connectors: They act as the interface between various components, allowing seamless connection and disconnection when necessary.
•Terminals: These are the endpoints of wires or cables, which are crimped or soldered to connectors for secure electrical contact.
•Protective Coverings: Insulating materials such as heat-shrink tubing, wire looms, or braided sleeves protect the wires from abrasion, moisture, and other environmental factors.
3.The Role of Wire Harness Assembly in Modern Electronics:
•Reliable Signal Transmission: Wire harnesses ensure efficient and reliable transmission of signals, minimizing signal loss and interference, which is crucial for optimal performance in sensitive electronic devices.
•Simplified Installation: By consolidating multiple wires into a single harness, the installation process becomes more straightforward and less time-consuming.
•Space Optimization: Wire harnesses enable efficient utilization of available space within electronic systems, reducing clutter and enhancing overall design flexibility.
•Enhanced Durability: Properly assembled and protected wire harnesses increase the durability and longevity of electronic equipment, reducing the risk of premature failures due to wire damage or connection issues.
4.The Flex Circuit Manufacturing Process: Flex circuits, also known as flexible printed circuit boards (PCBs), are integral components of wire harness assembly. These circuits are made from thin, flexible substrates, allowing them to bend, twist, or fold, enabling greater design versatility and space optimization. The flex circuit manufacturing process involves:
•Substrate Preparation: The flexible substrate material, typically polyimide or polyester, is prepared and coated with a conductive layer.
•Circuit Patterning: The conductive layer is selectively etched to create the desired circuit pattern, which defines the electrical pathways.
•Component Assembly: Electronic components such as resistors, capacitors, and integrated circuits are mounted onto the flex circuit using advanced surface mount technology.
•Testing and Inspection: The flex circuits undergo rigorous testing and inspection to ensure functionality and quality.
Conclusion: Wire harness assembly, along with the flex circuit manufacturing process, is an unsung hero in the world of modern electronics. It provides the necessary structure, organization, and connectivity for electronic systems to function seamlessly. Whether it's a complex industrial machine or a sophisticated medical device, wire harness assembly manufacturers like NorthPointech play a critical role in enabling innovation and driving technological advancements.