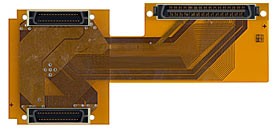
Fast and ahead, so is the world of electronics manufacturing, with local printed circuit board producers seeking further ways to improve productivity while lowering costs. Against the backdrop of this surge in demand for PCB board manufacturers near me, businesses are applying such cutting-edge tactics to remain at the forefront of competition. Let's examine some of the innovative strategies being used to increase productivity without breaking the bank.
1.Industry and Automation 4.0 Adoption
One of the popular tools that regional PCB makers have started to use much more is automation for the optimization of their manufacturing procedures. They can do the following:
•Reduce human error and enhance precision;
•Increase the speed of production without the loss of quality;
•Reduce material waste;
•Have the possibility of producing 24/7 with an investment in smart, manufactured systems.
For many PCB makers, though usually huge in terms of an initial investment, automation is something very desirable because of the savings in costs and efficiency in the long run.
2.Lean Manufacturing Implementation
The PCB board manufacturers are trying to implement the lean manufacturing philosophy that was first developed by Toyota as a way of conducting business without waste and maximizing efficiency. Some of the strategies are:
• Just-in-time manufacturing to reduce inventory costs
• The 5S workplace organization technique that will ensure a more efficient working environment;
• Value stream mapping to identify and eliminate non-value-adding activities;
• A culture of continuous improvement in making constant process improvements.
These guidelines aid regional producers in cutting costs without sacrificing output standards or delivery schedules.
3.Harnessing Advanced DFM Software
Advanced DFM software is being utilized by PCB manufacturers to identify potential manufacturing problems very early in the design stage of a product. This proactive approach:
• Saves time and money on redesigns
• Cuts down on manufacturing errors and delays
• Improves first-pass yield rates
• Improves the quality of the overall product
Manufacturers can detect issues before they reach the factory floor, avoiding losses and improving efficiency.
4.Modular Production Systems
It forces local PCB manufacturers to adopt flexible manufacturing methods to meet the vast needs of their customers. They can
• Easily switch from one type of product to another.
• Produce efficiently in small and large batches using this strategy.
• Reduced set-up time between production runs;
• Better utilization of the equipment
Through the flexibility of their production processes, such organizations can continue to enjoy high efficiency even while serving an expanded customer base.
5.Making Training and Development Invest in Staff
Recognizing the value of their people, progressive PCB manufacturers invest in comprehensive training programs. This strategy-
• Reduces errors and rework
• Enhances problem-solving capabilities on the shop floor
• Staff satisfaction and retention
• Staff skills and efficiency
A well-trained employee significantly contributes to overall productivity and usually finds cost-reducing opportunities in his regular work.
6.Energy-Efficient Technologies Implementation
The local manufacturers of PCBs target energy efficiency due to the increasing energy bills as a cost-reduction strategy. The strategies are as follows:
• During industrial processes, heat recovery systems should be installed.
• Smart power management system installation
• Purchase of energy-efficient manufacturing equipment
• Setting up energy-efficient lighting and heating-ventilation-air-conditioning systems
These actions come not only with the view of cutting down on operational expenses but also respond to the growing "green" concerns of consumers.
7.Collaboration with Local Suppliers and Customers
The regional producers of the PCB board have started to strengthen their relationships with customers along with the regional supply chains. It has several benefits, such as:
• Lower lead times and shipping expenses;
• More efficient collaboration and communication on design
• Quicker response to the needs of the clients and market changes;
• The ability to allow collaborative creativity and problem-solving
Close relationships locally can help manufacturers make more responsive and lean supply chains.
Conclusion
Local double-sided PCB manufacturers are working up productivity in all ways possible to survive in this cutthroat market by adopting a variety of strategies in an enterprising and cost-effective way. State-of-the-art technologies and regional partnerships implement the concepts of lean, through which these businesses are now figuring out how to turn out better products at competitive prices and speeds.